News
The latest news from Scott Bader around the world.
Scott Bader's news from around the world, covering composites, adhesive and functional polymer news and developments.
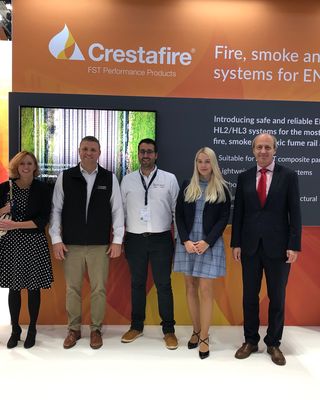
Scott Bader prepare to exhibit across Europe, Asia and North America in the coming months
Visit the Scott Bader team across various industry shows
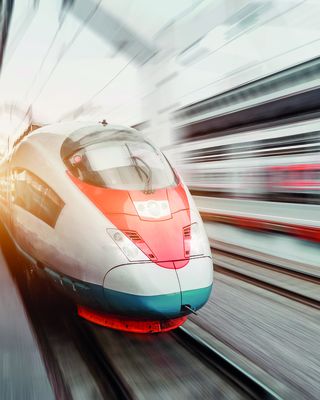
Scott Bader to showcase 100% bio-based fire-retardant resins at InnoTrans 2024
Scott Bader to showcase 100% bio-based fire-retardant resins at InnoTrans 2024
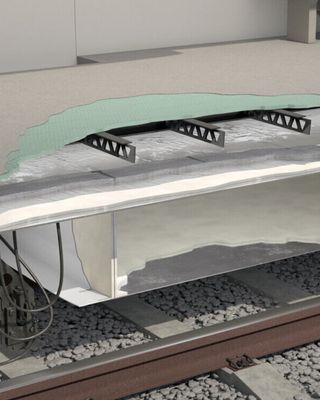
New sustainable composite flooring solution for rail
New sustainable composite flooring solution for rail
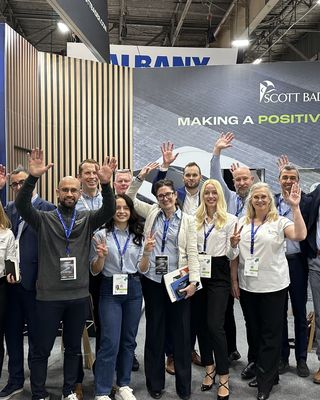
Scott Bader debuts marine & rail developments at JEC World 2025
Scott Bader debuts marine & rail developments at JEC World 2025
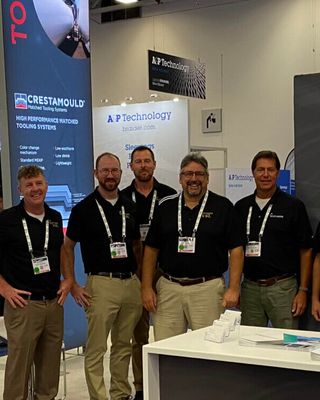
Scott Bader exhibiting across Europe, North America and Asia
Scott Bader teams across Europe, North America and Asia Pacific are preparing to exhibit their innovative composites, adhesives and functional polymers at a number of upcoming industry shows.
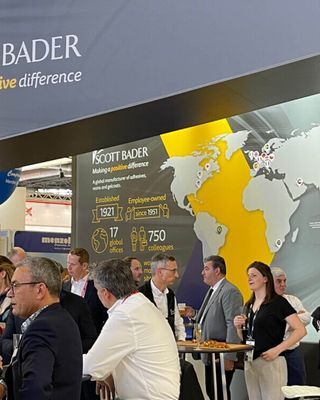
Scott Bader continues exhibition trail across UK, Turkey, Dubai and US
Scott Bader teams across Europe, Middle East and North America are preparing to exhibit our advanced composites and structural adhesives at a number of upcoming industry shows.
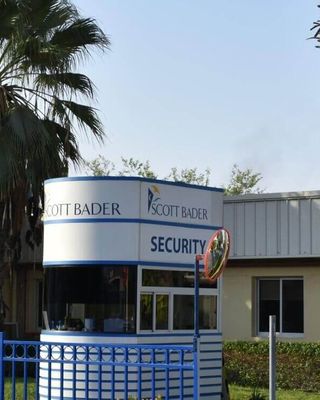
Scott Bader Middle East announce change to their working week
Scott Bader Middle East have switched their working week to Monday to Friday, effective from 3rd January 2022.
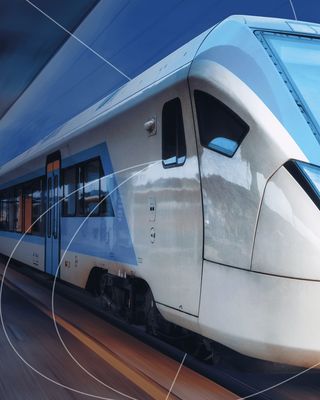
Scott Bader Pty join Rail Manufacturers Cluster to drive fire safety standards in South Africa
Scott Bader South Africa have recently joined the Rail Manufacturers Cluster of South Africa.
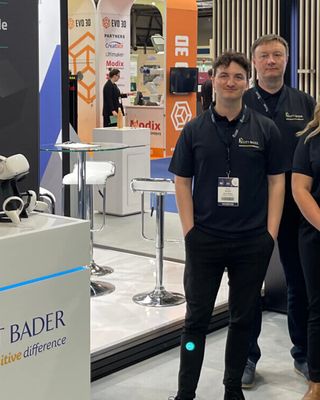
Scott Bader teams prepare for exhibitions across Europe and US
Visit the Scott Bader team across various European and US industry shows

Scott Bader North America exhibiting at CAMX 2021
Scott Bader North America are excited to return to CAMX in 2021
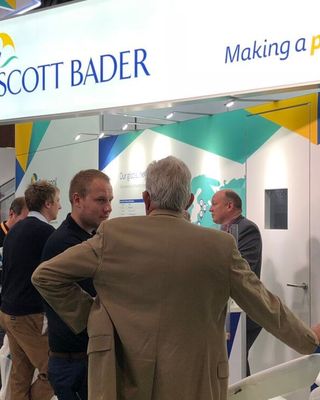
Scott Bader UK exhibiting at Advanced Engineering
Scott Bader UK exhibiting at Advanced Engineering
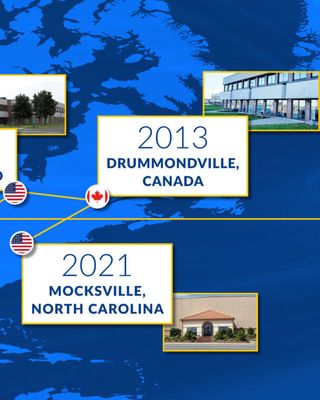
Scott Bader Inc celebrates 30-year anniversary
Celebrating 30 years of Scott Bader Inc